Innovative Manufacturing Processes
Kosei’s never ending search for new innovations has resulted in the birth of a new production process, a complete line of producing wheels from casting to machining. The process integrates high speed casting, flow forming, friction welding and high speed heat treatment process
Super Forming
High-strength and lightness is achieved thru Super Forming process. Rim thickness can be reduced up to 3.5mm while increasing elongation property of the rim by up to 10% comparable to a forged rim
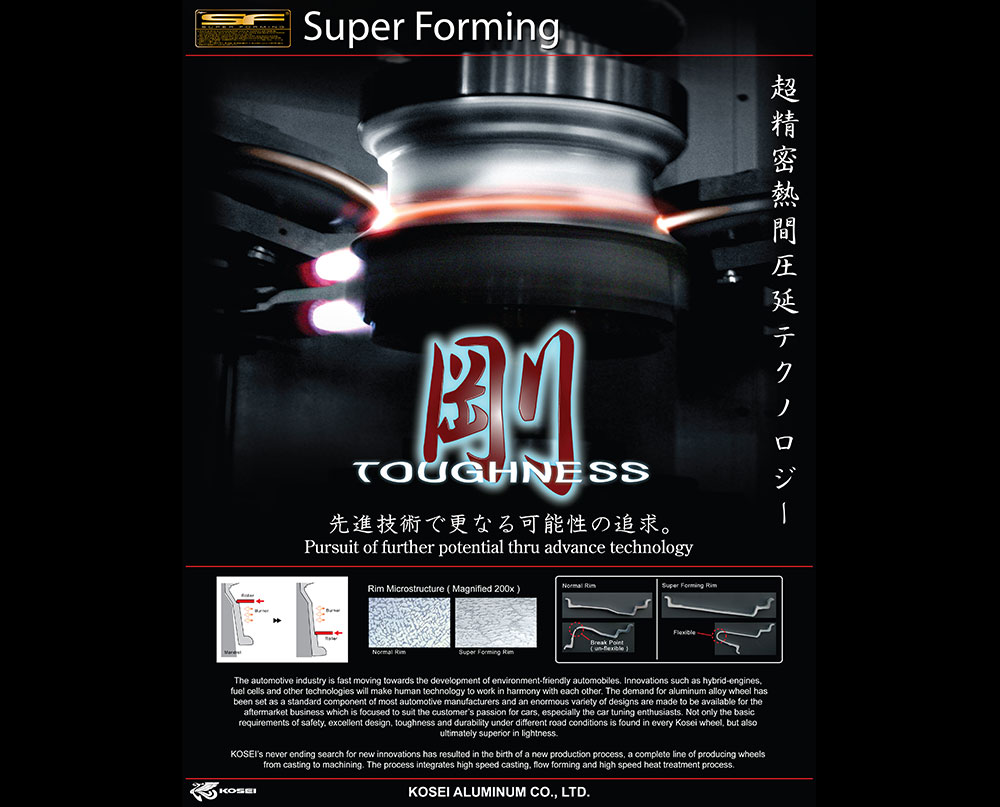
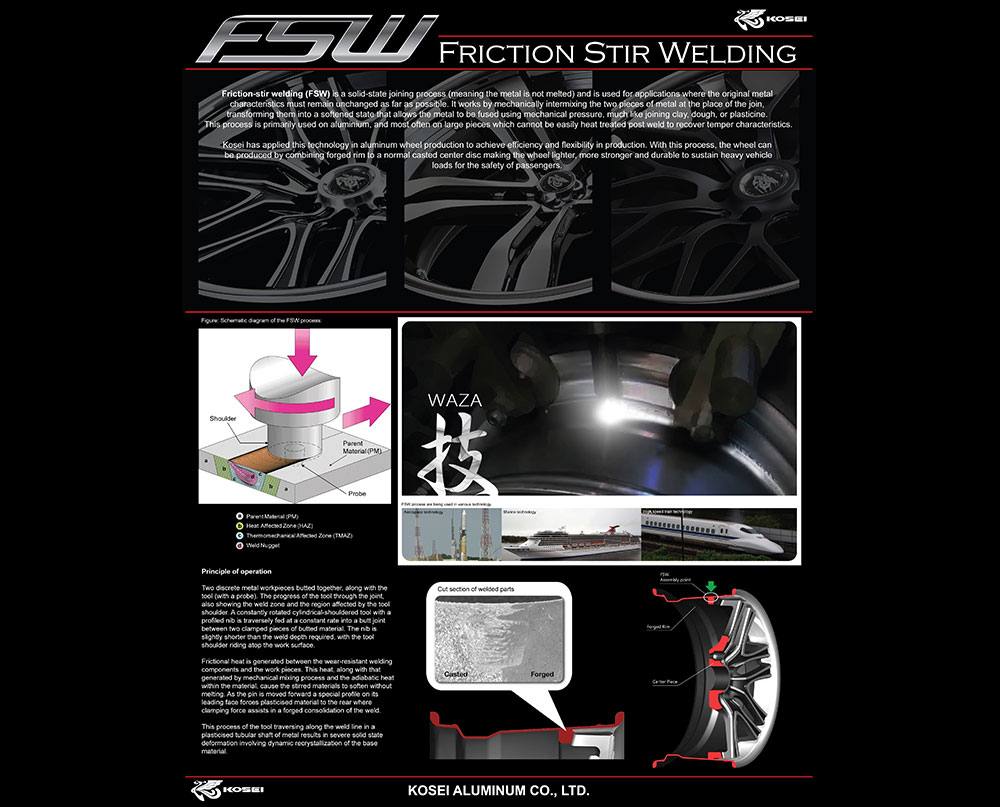
Kosei Friction Technology
Up to 25% weight reduction of wheel is possible with Kosei Friction Technology. Two separate wheel part (Disk and Forged Rim) is joined together as one, the result is a strong, light and durable wheel made possible only thru KFT.
Max Cooling
Reduced casting time leads to increased production rate while keeping wheel production cost down. Achieved only thru Kosei’s Max Cooling Technology, up to 40% reduction in casting cycle time can is possible by using specially designed mold with cooling jackets for faster and efficient cooling of aluminum cast wheel
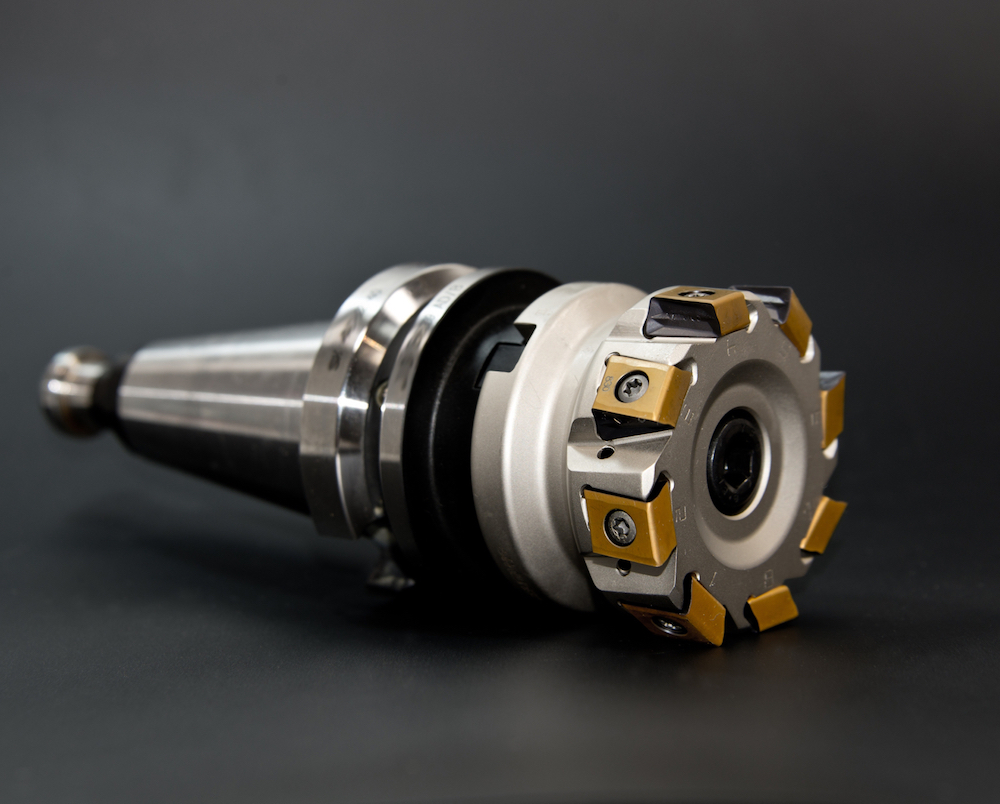
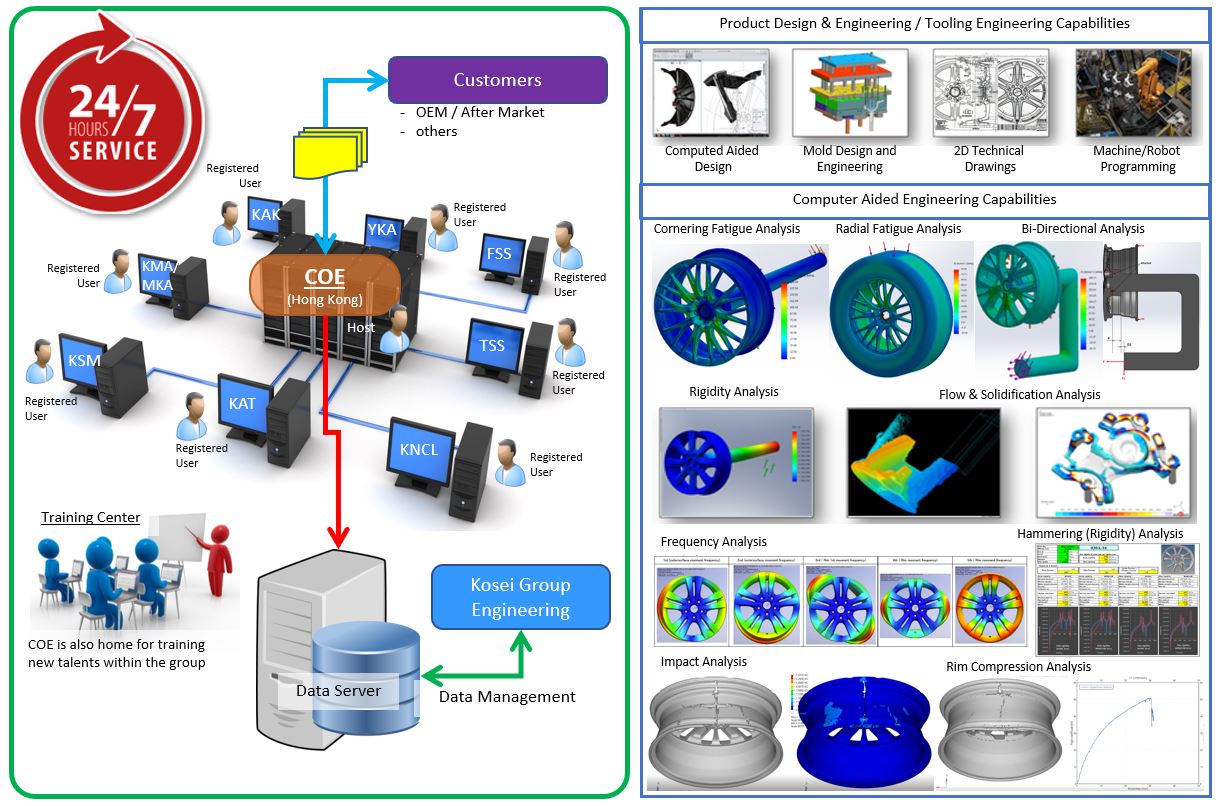
COE
COE or Center of Excellence was established by KOSEI to be the center of all design, engineering anddevelopment to provide technical support within entire KOSEI group